Чтобы приготовить из чугуна
ковкое железо, необходимо удалить из него углерод, т. е. подвергнуть его дальнейшей обработке, которая у металлургов получила название «кричный передел», или «фришевание» (от немецкого слова
frisch—свежий, здоровый, чистый) либо «рафинирование» (от французского
raffiner—очищать).
Открытие и освоение такого способа обработки позволило постепенно перейти от кричных сыродутных горнов к рудоплавильным печам—домницам.
В них стали получать жидкий чугун, который затем превращали в мягкое железо,а позднее—в сталь(удаляя избыточный углерод).
Так возник
двухступенчатый—через промежуточный продукт (чугун)—способ производства стали.
Это типичный пример того, как простое увеличение размеров оборудования, в данном случае сыродутных горнов, может привести к принципиально новой технологии.
Вместе с ростом потребности в ковком железе и стали постоянно возрастал спрос и на древесный уголь, однако в богатых рудой районах леса были вырублены.
Особенно заметно это было в Англии.
Но шахтные печи для выплавки чугуна (теперь их называют домнами), как и печи для дальнейшего его передела, нуждались в древесном угле.
В
1709 г. Абрахаму Дерби
из английского города Колбрукдейл впервые удалось применить в доменной печи каменноугольный кокс и тем самым модернизировать первую ступень процесса производства стали.
Однако для переработки чугуна в сталь по-прежнему был необходим древесный уголь.
Каменный уголь тогда еще не умели использовать для этой цели: содержащаяся в нем сера переходила в сталь, делая ее непригодной.
Проблему решил англичанин
Генри Корт
в 1784 г. Изобретенный им способ
пудлингования (от английского
рuddlе-месить, перемешивать) означал новый большой шаг вперед, и это по праву можно считать началом современной металлургии стали.
В пудлинговой печи топливо уже не соприкасается с чугуном, подлежащим переработке.
Каменный уголь сгорает в топке, которая отделена от горна порогом.
Первые пудлинговые печи имели две дымовые трубы: одну непосредственно над топкой, другую с противоположного конца печи, над плавильным горном, или ванной.
Пудлингование—это очистка чугуна в пламенной печи.
Процесс начинается с загрузки чугуна в горн. Чтобы ускорить плавку, куски чугуна весом 10—30 кг (всего обрабатывается около 150 кг) помещают вблизи порога топки, где температура самая высокая.
Примерно через 45 мин чугун расплавляется.
Пудлинговщик вставляет в загрузочное окно печи железную штангу с крюком на конце и проводит ею борозды по тестообразной чугунной массе (массу металла, расплавленного в печи, металлурги называют ванной).
При этом чугун хорошо перемешивается и поверхность ванны увеличивается. Закрывая горн и забрасывая влажный шлак, пудлинговщик регулирует температуру ванны.
Кроме того, в ванну добавляют песок, который, вступая в химическую реакцию с футеровкой печи, образует шлак; последний окисляет углерод в чугуне. В период кипения ванна сильно бурлит за счет окисления углерода, и чем больше его окисляется, тем сильнее разжижается ванна, и железные зерна собираются там в комья.
Пудлинговщик ломом много раз переворачивает массу и наконец разделяет ее на три-пять частей—криц.
Они еще горячими попадают к кузнецу, который к каждой крице приваривает железный стержень дюймовой толщины и проковывает их в «колбаски» диаметром 7—10 см и длиной около 50 см.
Эти заготовки в прокатной машине раскатывают в полосы, затем снова разделяют на куски длиной 50 см и еще раз прокатывают, накладывая по 4 полосы одна на другую. Для процесса пудлингования были характерны именно эти операции прокатки криц, которые требовались не столько для придания заготовке формы, сколько для того, чтобы сварить зерна и комки железа. В результате получалось так называемое сварочное железо (или сварочная сталь).
Одна пудлинговая печь за сутки давала 3500 кг крупнозернистого кричного железа либо 1600 кг мелкозернистого железа— пудлинговой стали.
Пудлингование означало существенный прогресс по сравнению с прежним сыродутным способом и кричным переделом.
Во-первых, вместо дефицитного древесного угля теперь можно было обходиться каменным углем.
Во-вторых, пудлинговые печи оказались намного производительнее. И наконец, в результате пудлингования получали сварочное железо (или сварочную сталь)—материал с отличными свойствами.
Насколько высоко ценилось сварочное железо, можно судить хотя бы по тому, что уже после изобретения процессов производства литой стали металлурги искали и нашли способ приготовления из нее «искусственного» сварочного железа.
Американцы, в частности, заметили, что сварочное железо в мостах и других сооружениях под открытым небом втрое устойчивее к коррозии, чем литая (или прокатанная из слитков) сталь.
Поскольку приготовление сварочного железа в пудлинговых печах стоило слишком дорого, был разработан специальный метод производства сварочного железа из литой стали.
Это
«астон-железо», названное так по имени его изобретателя и по своим свойствам не уступавшее сварочному. Его изготовляли и применяли еще до второй мировой войны.
В пудлинговой печи топка отделена порогом от очищаемого чугуна. Поэтому здесь вместо древесного угля можно использовать каменный уголь или кокс, не опасаясь загрязнения железа серой, присутствующей в каменном угле в больших количествах.
Однако сварочное железо и сварочная сталь имели и серьезный недостаток—неравномерность состава по поперечному сечению.
Английский часовщик
Бенджамин Хантсмен
(1704—1776) пришел к мысли, что
состав этих материалов можно выровнять путем переплавки.
Эта идея была не нова, и раньше не раз пытались таким путем улучшить однородность и качество сварочной стали, но безуспешно.
Чтобы получить жидкую сталь,
Хантсмен использовал тигель из огнеупорного материала и обогреваемую коксом печь с дутьем и высоким горном.
Это принесло успех. Французские кузнецы первыми изготовили из литой стали, твердой и потому труднее поддающейся ковке, ножи, которые оказались лучше шеффилдских.
Старшины шеффилдского цеха кузнецов обратились в палату общин английского парламента с просьбой запретить вывоз из страны литойстали. Их просьба была отклонена. Тогда шеффилдским кузнецам пришлось преодолеть свое предубеждение против литой стали. Производство стальных изделий в Англии стало быстро развиваться, и вскоре по этому показателю она вышла на первое место в мире. Значительно расширился экспорт не только готовых стальных изделий, но и стальных слитков.
Высококачественная тигельная сталь обладала превосходными свойствами в литом состоянии. Спустя столетие после изобретения Хантсмена из нее стали делать паровозные оси, а еще позже
- орудийные стволы.
В 1851 г, на Лондонской всемирной выставке был показан стальной слиток весом 2150 кг. Чтобы получить такую большую отливку, пришлось сливать в миксер (копильник) расплавленную сталь из многих тиглей емкостью по 45 кг каждый.
В эпоху промышленной революции потребность в железе настолько сильно возросла, что ее не мог удовлетворить и пудлинговый процесс. К тому же различные новые технические применения пудлингового железа показали, что оно не выдерживает больших нагрузок. Например, так как железнодорожные локомотивы становились тяжелее и быстроходнее, рельсы, изготовленные из пудлинговой стали, все чаще ломались.
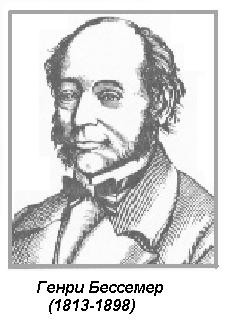
Основателем сталеплавильного производства следует считать
Генри Бессемера
(1813—1898).
В 1885 г. он впервые получил ковкое железо, вернее сталь, путем
продувки воздухом 5 кг сырого чугуна, расплавленного в тигле из огнеупорной глины.
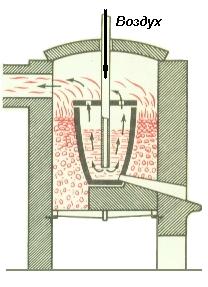
Оказалось, что при продувке воздухом расплавленный чугун не только не охлаждается, как предполагали прежде, но, напротив, его температура возрастает настолько, что ванна остается жидкой, хотя сталь, которая образуется из чугуна благодаря продувке, имеет более высокую температуру плавления. 17 октября 1855 г.
Бессемер получил английский патент на свое изобретение.
Прусское патентное ведомство в Берлине отказалось выдать ему патент, мотивировав свой отказ следующим образом: «Нельзя никому запретить продувать воздух через жидкое железо».
Вот весьма выразительный пример непонимания сущности технического прогресса.
Новый процесс получения стали из чугуна «без топлива и без топки» прошел длинный, усеянный множеством неудач путь, прежде чем стало ясно, что хорошую сталь дает только малофосфористый чугун. Если же в чугуне много фосфора, то продукт получается хуже, чем ковкое железо,—он оказывается пористым «красноломким» и «холодноломким» (т.е. хрупким в горячем и в холодном состояниях).
Вследствие этих сложностей бессемеровский процесс распространялся весьма медленно—сначала он был принят в Швеции, затем—в Австрии и только позднее—в Англии. Широкому его распространению препятствовало то, что он нуждался в малофосфористом чугуне. В результате главной проблемой стала очистка чугуна от фосфора.
Среди многих металлургов, которые пытались решить эту проблему, первым достиг успеха
Сидней Джилкрист Томас
(1850-1885).
Томас имел две специальности. Он служил писарем в лондонском полицейском суде, чем зарабатывал на жизнь, и одновременно изучал химию и металлургию в Горном училище, где и заинтересовался проблемой удаления фосфора из чугуна. В 1877 г. Томас подал первую заявку (а в 1878—1879 гг.—еще две) на способ получения стали, который позднее был назван его именем.
Непосвященный не увидит особой разницы между бессемеровским и томасовским процессами.
В основе обоих процессов лежит один и тот же принцип: чугун, из которого получают сталь, очищают, продувая через него воздух.
Сосуд, где протекает реакция,—конвертер—имеет грушевидную форму с открытой горловиной вверху; он укреплен на горизонтальной оси, что позволяет его наклонять. Конвертеры Бессемера и Томаса по внешнему виду одинаковы. Главное различие заключается в том, что
бессемеровский конвертер изнутри выложен
- кислой (т. е. кислотной по своему химическому характеру) огнеупорной футеровкой и в нем нельзя удалить фосфор из богатого им чугуна в основной шлак (т. е. по своим химическим свойствам подобный основаниям), потому что такой шлак быстро разъедает кислую футеровку.
Томасовский же конвертер имеет основную футеровку, поэтому здесь, добавляя известь, можно получить
основной шлак, который хорошо извлекает фосфор из чугуна, но не разрушает
основную
футеровку.
Конвертерное производство стали в прошлом веке. Пока в левый конвертер заливают из ковша жидкий чугун, в правом идет процесс плавки.
В центре—готовую сталь разливают в изложницы.
Конвертер—будь то бессемеровский или
томасовский—позволяет за 20 мин превратить в сталь до 20 т чугуна. Для производства такого же количества стали в горне способом кричного передела потребовалось бы три недели, а в пудлинговой печи—неделя.
Так металлурги получили в свое распоряжение два высокопроизводительных процесса, что позволило удовлетворять непрерывно возрастающий в промышленных странах спрос на сталь. Бессемеровский и томасовский конвертеры были необходимы для массового производства стали общего назначения, тогда как высококачественные специальные стали продолжали выплавлять в тиглях.
Но техника не стояла на месте.
Братья Вильгельм и Фридрих Сименсы
изобрели
регенеративный способ обогрева печей и, после того как
Фридрих Сименс
получил патент на это изобретение, построили опытную печь. Основная идея регенеративного обогрева заключается
в предварительном подогреве воздуха, необходимого для горения топлива,
отходящими газами-продуктами горения. Для этого через определенные промежутки времени воздух направляют то через один, то через другой регенератор (пока воздух для горения, проходя через один регенератор и охлаждая его, сам нагревается, отходящие газы подогревают другой регенератор).
В опытной печи братьев
Сименсов стальные напильники через 6 ч расплавились, а тигель, помещенный в топочную камеру, превратился в шлак.
Первые практические попытки выплавить тигельную сталь в подобной печи на сталелитейном заводе в Шеффилде закончились неудачей.
Вместе со сталью плавились тигель и стенки печи.
8 апреля 1864 г. на одном из заводов Южной Франции
Пьеру Мартену
(1824—1915) впервые удалось сварить хорошую сталь в регенеративной печи, построенной при участии
Вильгельма Сименса. Шихта (загружаемые в печь исходные материалы) состояла из чугуна, выплавленного из гематита—красного железняка с острова Эльба, чушек пудлингового железа и стального лома.
Мартеновский процесс (немцы его называют
сименс-мартеновским) наряду с
бессемеровским
и томасовским ознаменовал еще один важный шаг в развитии сталелитейного производства1. Этот процесс сохранил большое практическое значение до наших дней; особенно широко он используется для повторного производства стали из лома и стальных отходов (как говорят металлурги, из «скрапа»).
Интересно заметить, что Генри Бессемер изобрел свой конвертер, а Вильгельм Сименс—регенеративную печь примерно в одно и то же время, живя на соседних улицах в Лондоне и ничего не зная друг о друге.
Новый процесс получил широкую известность после Парижской выставки 1867 г.
В России первую мартеновскую печь построили в 1869—1870гг. на Сормовском заводе А.А.Износков и Н.Н. Кузнецов.
Наконец мир избавился от «стального голода».
Получив в свое распоряжение такие высокопроизводительные технологические процессы, Англия благодаря изобретениям Бессемера и Сименса упрочила свое положение ведущей промышленной державы.
Уже в 1870 г. производство стали в Англии превысило 5 млн. т и продолжало быстро расти.
Таким образом, за столетие был достигнут примерно стократный прирост: во второй половине XVIII в. в Англии производилось за год порядка 50—100 тыс. т стали.